Aluminum Die Casting: Manufacturing Solution for Durable Components
Aluminum die casting is one of the most widely used methods for producing precise, durable, and complex metal parts. Known for its excellent strength-to-weight ratio, corrosion resistance, and ability to be molded into intricate shapes, aluminum die cast has become an essential manufacturing process across various industries, including automotive, aerospace, electronics, and consumer goods.
What is Aluminum Die Casting?
Aluminum die casting is a metal casting process in which molten aluminum is injected into a steel mold (also called a die) under high pressure. The aluminum then cools and solidifies, taking the shape of the die. Once the casting has cooled, the die is opened, and the finished part is ejected.
This process allows manufacturers to produce high volumes of complex and precise parts with tight tolerances and superior surface finishes. It’s a versatile technique that can accommodate a wide range of aluminum alloys, each offering distinct properties for different applications.
Advantages of Aluminum Die Casting
- High Precision and Complexity
Aluminum die casting is known for producing parts with intricate designs, fine details, and tight tolerances. The pressure injection process ensures that the molten aluminum fills every cavity in the mold, allowing for the creation of highly complex shapes that would be difficult or impossible to achieve using traditional casting methods. - Lightweight and Strong
Aluminum is a lightweight metal, making it ideal for applications where weight reduction is essential without compromising strength. Aluminum die castings are known for their exceptional strength-to-weight ratio, which is particularly beneficial in industries such as automotive and aerospace, where lightweight parts are crucial for performance and fuel efficiency. - Corrosion Resistance
One of the standout features of aluminum is its natural resistance to corrosion. Aluminum forms a protective oxide layer on its surface when exposed to air, making aluminum die-cast components highly resistant to rust and degradation. This property is vital for parts exposed to outdoor elements, such as automotive components, outdoor lighting fixtures, and marine equipment. - Cost-Effective for High Volumes
While the initial setup for die casting can be expensive due to the cost of molds and tooling, it is an incredibly cost-effective process for producing high volumes of parts. Once the die is created, the per-unit cost of manufacturing is low, which is especially beneficial for industries that require large quantities of parts, such as the automotive and electronics industries. - Excellent Surface Finish
Aluminum die-cast parts often require minimal post-processing due to the excellent surface finish achieved during the casting process. The smoothness of the surface can be enhanced with processes such as polishing or coating, and the parts often have a high-quality, attractive appearance straight from the die. - Heat Dissipation
Aluminum is an excellent conductor of heat, making it ideal for applications where heat dissipation is important. Many electronics, automotive, and LED lighting components utilize aluminum die-cast parts for their ability to efficiently conduct heat away from sensitive components.
Applications of Aluminum Die Casting
Aluminum die casting is used in a wide array of industries, thanks to its versatility and reliability. Some common applications include:
- Automotive Industry: Engine blocks, transmission housings, wheel rims, and other critical components require lightweight, strong, and durable parts. Aluminum die casting provides solutions that meet these demands.
- Aerospace Industry: Aircraft parts, such as brackets, housings, and structural components, benefit from the strength and low weight of aluminum die castings.
- Electronics: Heat sinks, enclosures, and housings for electronic devices, such as computers, smartphones, and LED lighting systems, are often made using aluminum die casting.
- Consumer Goods: Household appliances, tools, and decorative items, like knobs and handles, are commonly made from aluminum die castings due to their high durability and ease of mass production.
The Aluminum Die Casting Process
- Mold Creation: The first step in the die casting process is creating a mold, or die, made from high-strength steel. The die is designed with cavities that match the shape of the desired component. Dies are typically precision-machined to ensure tight tolerances and high-quality results.
- Melting the Aluminum: Aluminum is heated in a furnace to its molten state, with temperatures reaching around 700-800°C (1292-1472°F). Once the aluminum reaches the correct temperature, it is ready to be injected into the mold.
- Injection: The molten aluminum is injected into the die under high pressure using a hydraulic or mechanical press. The high pressure ensures that the molten metal completely fills the mold cavity, eliminating air pockets and voids, resulting in a solid, high-quality part.
- Cooling and Ejection: After the aluminum is injected, it quickly cools and solidifies within the die. The die is then opened, and the finished part is ejected.
- Finishing: Depending on the application, the aluminum die-cast part may undergo further processes such as trimming, machining, polishing, or coating to meet the desired specifications.
Challenges and Considerations
While aluminum die casting offers many benefits, there are some challenges and considerations to keep in mind:
- Tooling Costs: The initial cost of tooling and molds can be high, particularly for complex parts. However, the per-unit cost decreases as production volume increases, making it cost-effective for large-scale manufacturing.
- Design Limitations: Although die casting allows for complex shapes, the design must consider draft angles and the ability of the molten metal to flow into the mold cavity. Parts with undercuts or intricate geometries may require additional considerations during the design phase.
Conclusion
Aluminum die casting is a reliable and efficient manufacturing process that produces high-quality, durable, and lightweight parts for a variety of industries. Its advantages, including precision, corrosion resistance, cost-effectiveness for high volumes, and excellent surface finish, make it the ideal choice for many applications, especially in automotive, aerospace, electronics, and consumer goods.
As technology continues to evolve, aluminum die casting remains a critical process in the production of complex, high-performance components, meeting the growing demand for quality, precision, and innovation across industries.
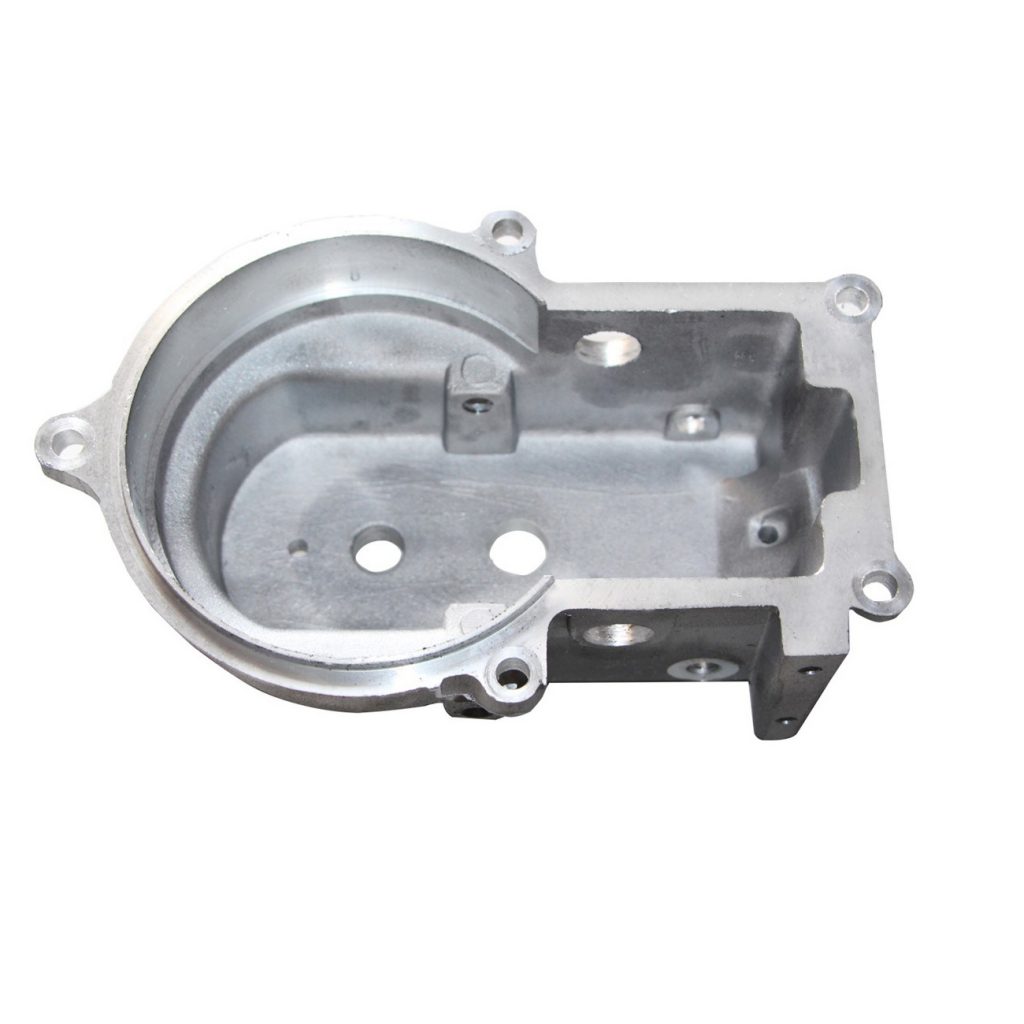